Winter 2023 Update
- Joey Evans
- Dec 25, 2023
- 4 min read
Updated: Feb 15, 2024
We have recently taken delivery of the leaf springs for the power bogie. Although these had been ordered at the same time as the trailing bogie springs their manufacture was not as pressing since further work will not commence on this until the trailing bogie has been completed. We have also ordered the volute springs which are needed for the couplings. Once these have been made and delivered we will have all the springs needed for GOWRIE. Moving on to the power bogie pivot assembly which it is intended to fabricate rather than being cast (see the excellent drawings by David Smith for this item), a suitable method of lubrication was discussed which has resulted in two further 3 feed oil boxes being cast, one of which can be seen being machined by Brian. Further work has been carried out by Stuart on the trailing bogie axleboxes. Each step in the machining is repeated on all of the castings before moving onto the next stage which will require a new setup. All four axleboxes have now had every face machined to within 1/16th of an inch of the finished dimensions. The final machining will take place once the hornguides have been fastened to the frames. In order to satisfy the requirements included in the Safety Verification documentation, Mark Brailsford of ABM NDT visited the workshop on Tuesday 24th October to carry out ultrasonic tests on the axles plus dye penetration test on the trailing bogie wheels. We were pleased to see that these tests gave satisfactory results. These tests having now been completed and the wheelsets for both bogies will now have more paint applied to a final finishing coat.

Power Bogie leaf springs freshly delivered (including one spare)

The two new oil boxes being machined for supplying oil to the power bogie pivot

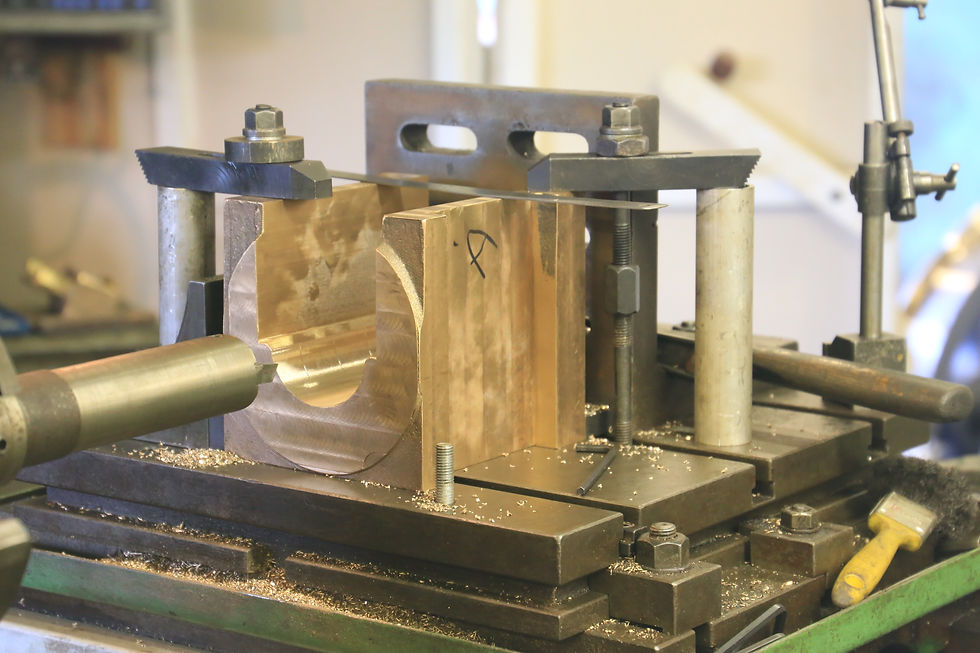
Trailing bogie axlebox being machined
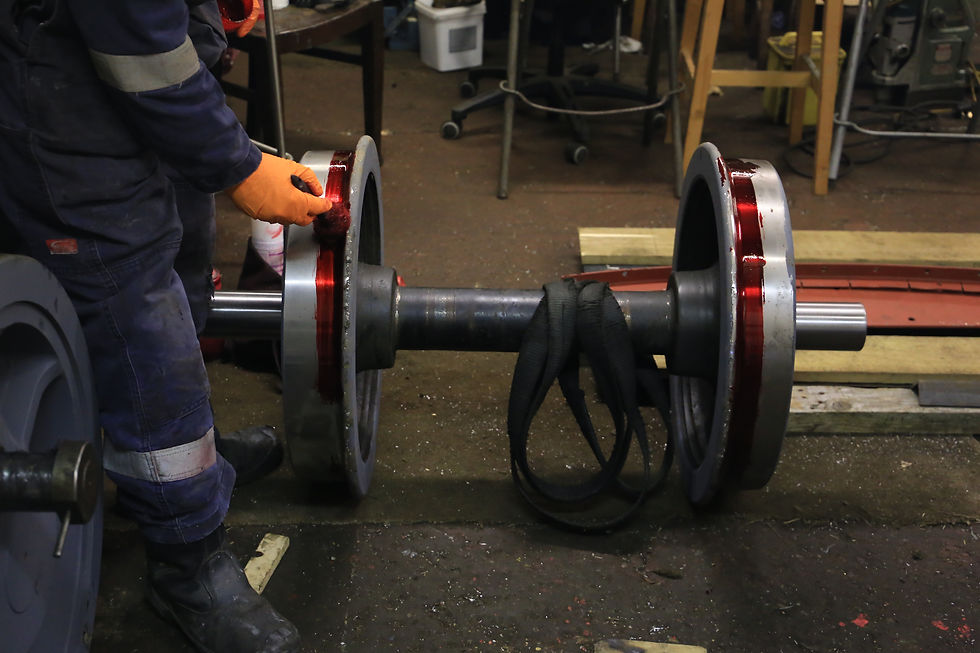
Dye penetration testing on trailing bogie wheelsets (1)

Dye penetration testing on trailing bogie wheelsets (2)

Trailing bogie frames being moved to the horizontal borer

Horn face openings being machined
On Thursday 9th November a visit was made to Greenbank Patterns to view and photograph the progress to date of the patterns for our cylinders. We were extremely satisfied with the excellent quality of these items and would recommend them for anyone needing the use of a good pattern maker. By the time you read this, the patterns will have been finished and delivered to the foundry in order for the cylinders to be cast. As you will see from the following images, the cylinder patterns are quite complex, since not only are they made up of several parts to form the main castings, there are several core boxes needed to enable the cylinder bores and steam passages to be made. Work is almost complete on the preparation of the side tank and bunker components in readiness for them being sent away for fabrication. This has entailed positioning and fixing the reinforcing strips for fastening the tanks down to their supports, also plates have been made and fitted to fix the balance pipe in its correct position behind the firebox. It is also intended to fit strainer boxes under the tanks in the same way as the ones fitted to 4-6-0 WD 303. Since the water feed from the tanks to the injectors was in a different place, on the inside face of the tanks, it has been necessary to find a suitable location to fix the strainer boxes in a location under the tank floors which does not interfere with any other parts. As it is the intention to fit vacuum brakes as well as the original air brakes, it will be necessary to find a suitable route to get the vacuum train pipe up into the cab for fixing to the ejector and brake application valve. This will take the form of a pipe welded into the right hand tank large enough to allow for some latitude in the position of the train pipe. It is hoped that a proper vacuum ejector and brake valve can be sourced, but provided the positioning of the tube is in the correct place for one to be fitted at a later date, it will be possible in the interim to use the system that was developed by Charles Adams, since we have access to these components.
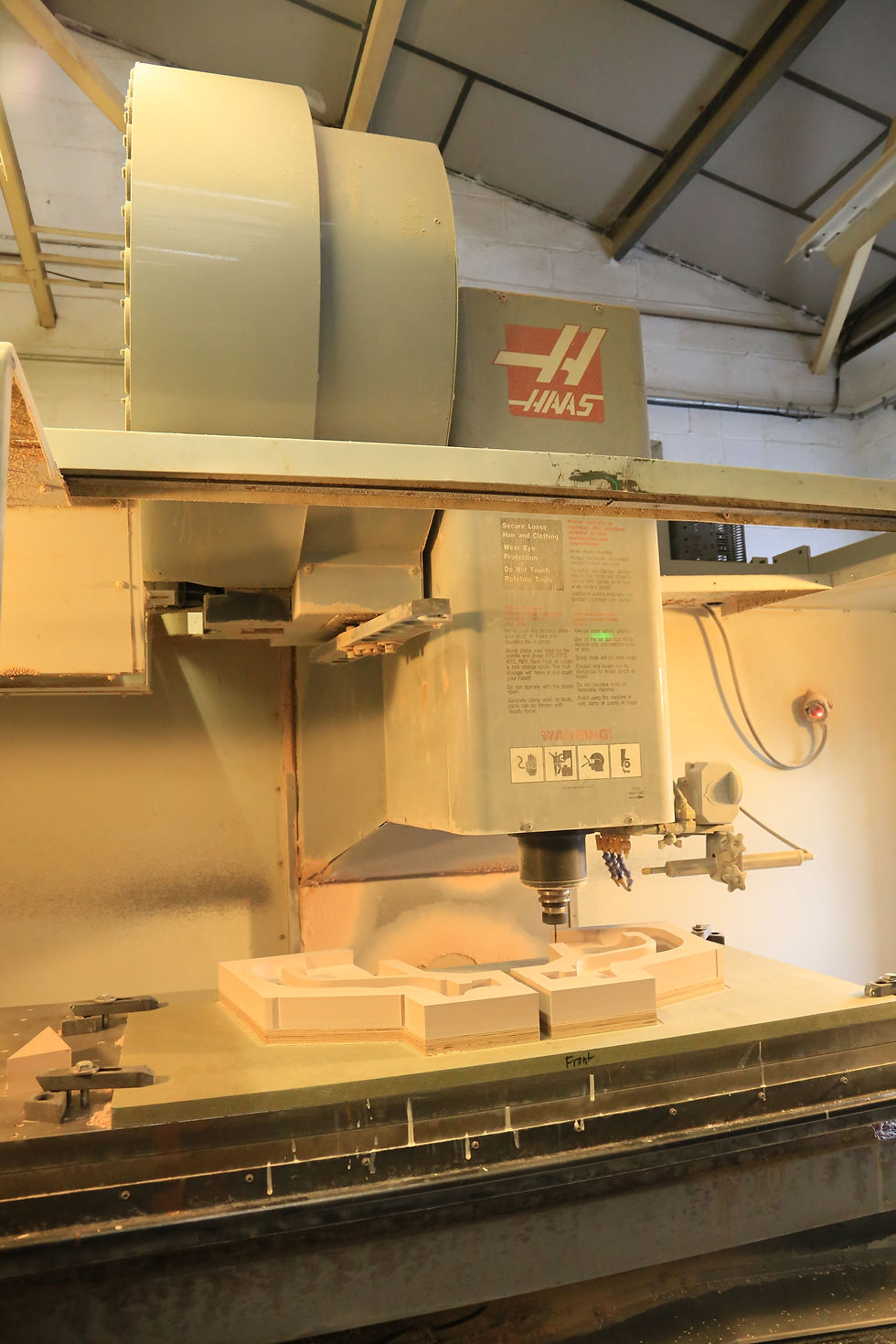
Both halves of one of the core boxes on the CNC machine

Close up view of the previous process
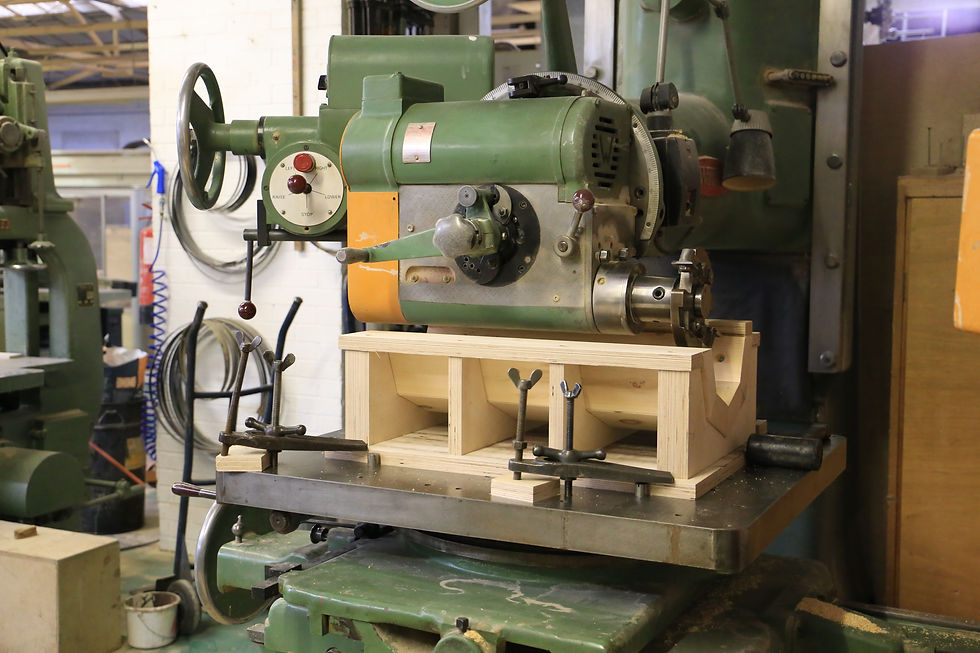
One half of the cylinder bore corebox set up for machining

Another view of the same setup
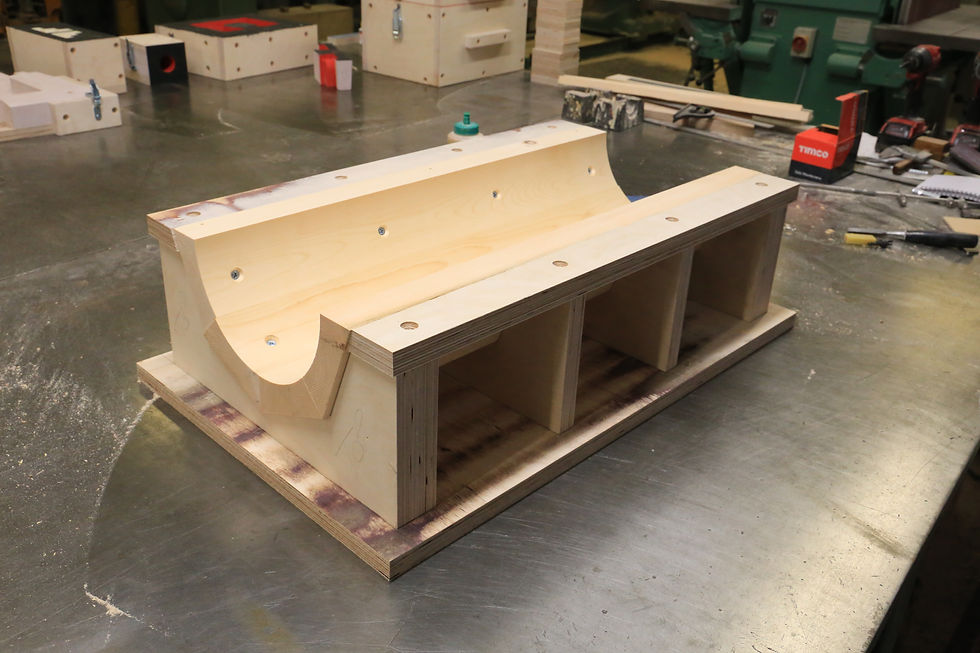
Half corebox machined

Corebox parts for the exhaust cavity

Inlet corebox parts

Half of the left hand cylinder pattern

Both halves of the right hand cylinder pattern

Right hand cylinder pattern together with the corebox supports
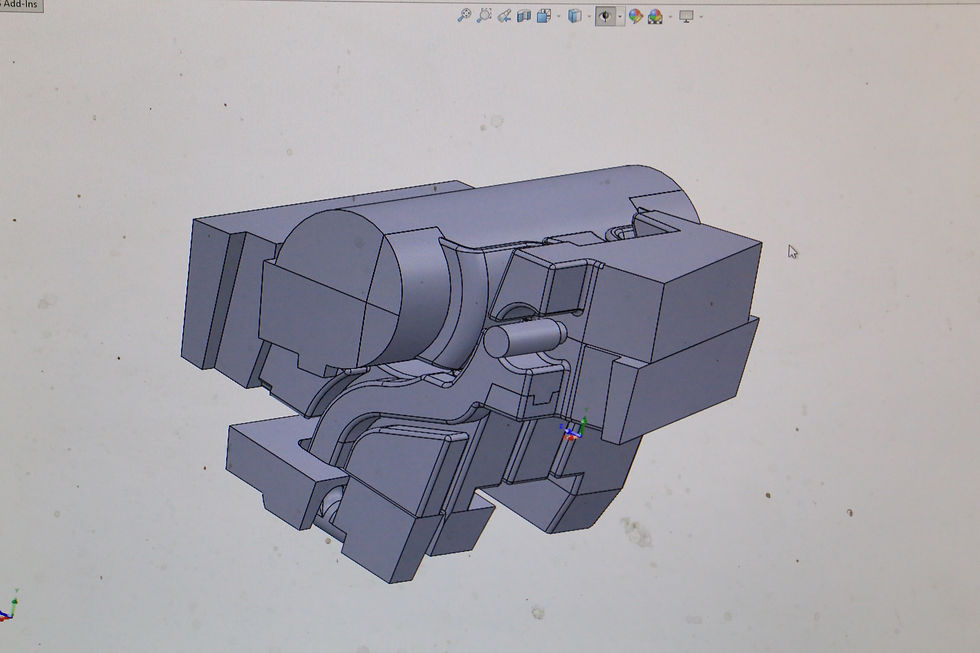
Screenshot of cylinder core assembly (1)

Screenshot of cylinder core assembly (2)
Power Bogie Pivot
Over the last few months discussions have taken place regarding the power bogie pivot assembly. On the original GOWRIE this consisted of two large castings, the upper one fastened to the carrier frames and supporting the boiler barrel, the lower one being fastened to the power bogie itself. A suggestion was made that we consider using fabrications instead of castings to produce these parts. After several meetings to discuss this, David Smith has produced the following drawings to illustrate the make up of these items. There is still some fine tuning required before we arrive at a design which can adequately and safely perform the function of the original castings. Once the design has been finalised these parts will be fabricated and machined by CTL Seal.

Kommentare